One-Stop Printed Circuit Board Fab & Assembly Solutions for Automotive Industry
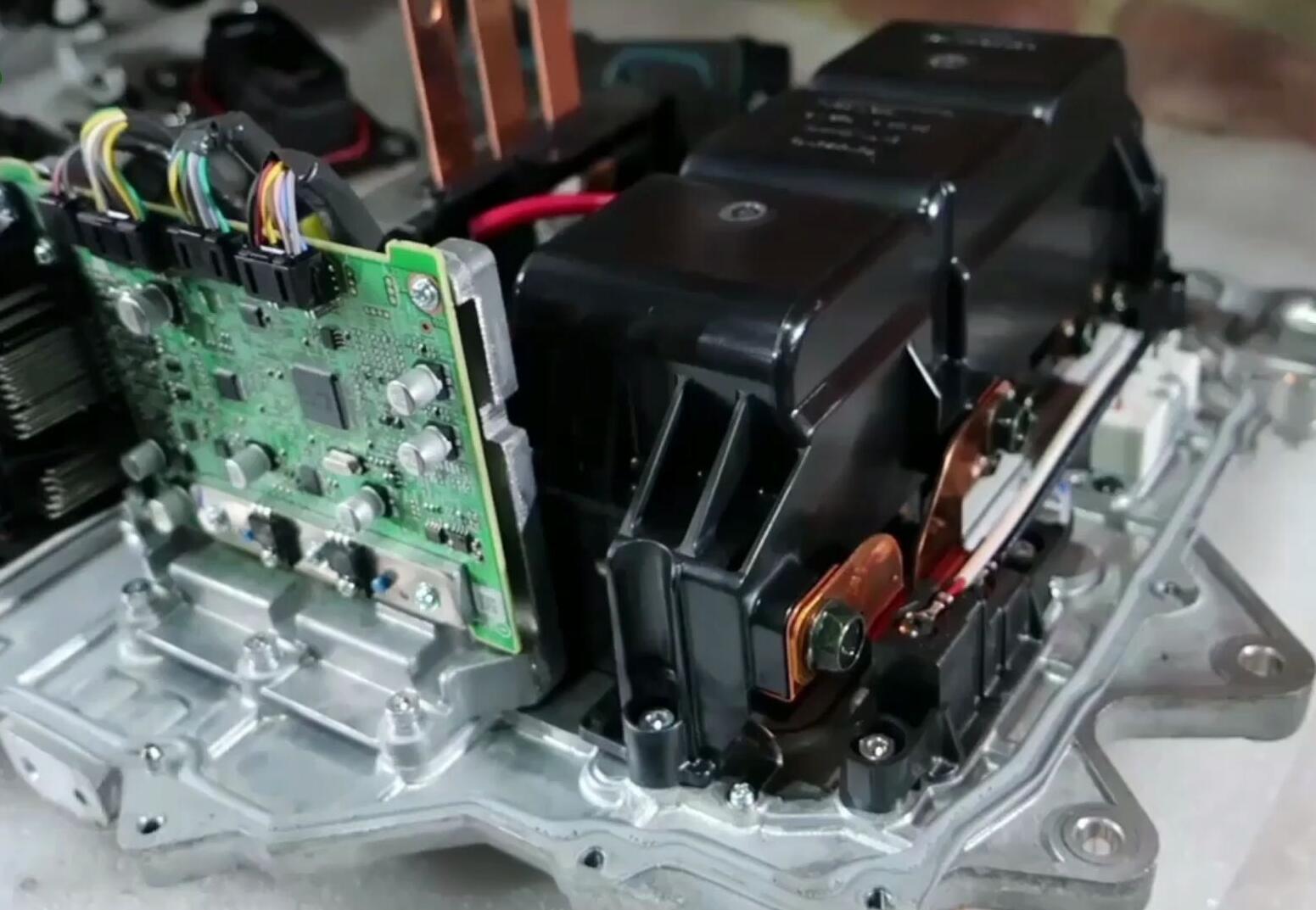
Description
Automotive PCB Assembly Manufacturing Services
What is Automotive PCB?
Automotive circuit boards include central control circuit boards, ignition control circuit boards, power amplifier circuit boards, audio-visual media player boards, etc. according to their function and region. Due to brand manufacturers, electronic buses, etc., many circuit modules and backplanes do not have a unified standard name.
With the increasing demand of consumers for the functionality, safety, comfort, and entertainment of automobiles, especially for autonomous driving, the proportion of hybrid electric vehicles and pure electric vehicles in new energy vehicles has also increased by a considerable amount. The demand for PCB circuit board products for new energy vehicles has also increased.
What Types of PCBs are Found in Automotive Electronics?
Electric vehicles have consistent, essential, and innovative requirements. Today, Tesla is leading the wave of innovation. However, innovations in electric vehicle manufacturing and design require durable, reliable, and rugged PCB applications. Therefore, this is difficult to do without professiopnal automotive PCB manufacturers. High-performance automotive PCB requirements can significantly withstand harsh driving conditions and could be a catalyst for innovation in the growing new energy drive systems.
Electric vehicle PCB demand mainly comes from powertrain-related equipment (vehicles, battery management systems (BMS), voltage conversion systems (DC-DC, inverters, etc.), and other high and low voltage devices). In addition, mmWave radar is an important sensing device for realizing intelligent and autonomous driving and has obvious advantages compared with other sensors.
High power copper plated PCB is one of the most widely good to use PCB applications in emerging industries. Flexible PCBs, HDI PCBs, and LED PCBs are good to use in AC/DC power converters, audio and video, digital displays, braking systems, automatic dimming, electronic mirror controls, automotive lighting, engine timing systems, and remote diagnostic systems.
Common Uses of PCBs in Automobiles
Circuit boards commonly found in automobiles are ones utilized for safety features. These are the boards that also require the utmost in reliability.
In particular, the circuit used for airbag deployment rate / crash sensors are invaluable in dissipating static electricity and triggering the airbag's deployment at the exact moment when it’s needed.
Other critical safety features often requiring high-reliability PCBs include anti-lock brake systems and sensors that would trigger such features.
More vehicle functions powered by boards include power converters, fluid monitors, engine timing, LED lighting, power distribution systems, on-board and remote diagnostics, security systems, and other sensors for non-critical situations (gas, tire pressure, and so on).
Audio/video equipment, touchscreens, and GPS systems are found in most modern automobiles and make use of boards to connect all the electrical components.
Automotive PCB Technologies
Our automotive customers select us for our expertise in advanced technologies. Technologies we have the capability to provide include the list below, as single-sided, double-sided, and multi-layer boards.
Metal core PCBs are good to use in circuits where a lot of heat appears. Similarly, heat needs to dissipate quickly so as not to damage components. During the operation of the circuit board, heat comes due to some electronic components.
The purpose of metal is to transfer heat from critical circuit board components to less important areas, such as the backing of a metal heat sink or the metal core. Therefore, these PCBs are easy to thermally manage.
When printed circuit boards were first put into practical use, the electrolytic copper foil was almost always good to use as a conductor material. The technique of forming metal by electroplating is electroforming, or electroforming for short.
Since thin copper foil is easy to produce inexpensively by the electroforming process, electrolytic copper foil eventually became the standard conductor material for printed circuit boards. Furthermore, it was good to use in large quantities.
HDI Automotive PCB Manufacturers
HDI PCB technology is also known as 'microvia', and sometimes as 'sequential build-up' or simply 'build-up' technology. We refer to it as HDI, following the approach of the IPC standard that defined it.
It come on on the use of via holes less than 150µm (0.006in) in diameter that can go to adjacent layers of a PCB without having to go through all layers, smaller then are easy to drill mechanically. It is commonly called a "microvia" and can be buried (buried microvia) or sealed (blind microvia).
Microvias come on by laser-drilling and through-plating vias between each pair of adjacent copper layers before they are glued together to make the finished PCB. When the end result is a via hole that only connects between internal copper layers, it is a buried microvia.
Rigid PCBs
FR4 rigid PCBs offer no flexibility and are often used for video screens and rear-view cameras. They are not ideal for high vibration placements or tight form fitting spaces.
Because of their flexible & durable nature, these PCBs can be used in automobile corners and bends. They’re made of polyester films, polyimide, or plastic.
The combination of the rigid board and the flexible board can not only provide the support of the rigid board but also have the bending characteristics of the flexible board. Therefore, it can meet the requirements of three-dimensional assembly.
Flexible-rigid boards are the most complex connecting structures in EA. A simple GZHP has one rigid and one flexible layer. Complex GBPs can have 20 or more connecting sets of oneway and two-way GBPs between rigid external PBs.
The creation of GPP and GZHP is due to the need to miniaturize EA; the disproportion between the volume and mass of ERP (unpackaged and surface-mounted components) placed on rigid PCBs and the volume and mass of rigid PCBs.
Ceramic substrate board is best for manufacturing single- and double-sided printed circuit boards with vias such as aluminum oxide and nitride. Generally, the technology has advantages over traditional thin-film and thick-film technologies for manufacturing ceramic printed circuit boards.
Single and double-sided printed circuit boards made using this technology come by high resolution, high electrical conductivity, solderability, and weldability along the switching tracks.
The manufactured ceramic printed circuit boards can be good to use for the manufacture of hybrid electronic circuits, in the field of the auto industry, optoelectronics, and microwave technology.
Why Choose Hitechpcba as PCB Assembly Solutions for the Automotive Industry
Automotive PCB assembly is a specialized process that requires experience and knowledge in order to produce high-quality results. There are many steps involved in the assembly process, and each one must be performed with precision and care. If even one step is done incorrectly, it can affect the performance and reliability of the finished product. Here are some reasons why choosing our automotive PCB assembly services is the best decision for your business:
1. Our PCBs meet the minimum tolerance requirements for RoHS, REACH and Conflict Minerals. We also have a variety of green certification programs, including ENIG, HAL and HASL.
2. We understand the importance of quality and reliability in PCBs, and we work hard to ensure that our products meet or exceed industry standards.
3. We have extensive experience in this field, and our team is composed of skilled and experienced engineers. We understand the unique challenges and requirements that this market demands. We use the latest technologies and equipment to ensure that our automotive PCB assembly services are of the highest quality.
4. We use only the highest quality components and materials in our PCB assembly process. This ensures the durability and reliability of your products. Our PCBAs can withstand heavy current loads. They are able to do this because of their excellent thermal conductivity, which helps dissipate heat and protect the components around them.
5. We have a comprehensive quality assurance system in place that guarantees the accuracy and consistency of your products.
At our company, we take great pride in the fact that we source all of our materials from trusted and reliable suppliers. We believe that this is what sets us apart from our competitors, and it’s something that we’re really proud of. We understand that our customers rely on us to provide them with high-quality products, and by working with only the best suppliers, we can ensure that we always deliver on our promise.
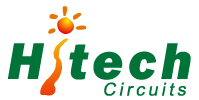
0086-755-29970700
sales@hitechpcb.com; sales@hitechcircuits.com
2F, Building C, Suojia Technology Park, Hangcheng, Bao’an, Shenzhen, Guangdong, China 518126