Teflon PCB
What is high frequency pcb?
As complexity of electronic components increases, the one thing that becomes imperative is signal rates and high frequency of transmission. Little surprise then that the demand for high frequency PCBs is on the rise. They find use in a variety of high-speed design applications that require a frequency range of 500MHz to 2GHz.
FR-4, based on epoxy resin and glass reinforcement, is the most popular laminate material for printed circuit board industry for a long time. The FR4 dielectric constant ranges from 3.8 to 4.8, depending on the glass weave style, thickness, resin content, and copper foil roughness. However, PCB industry also use other material for different application. In RF/microwave products, low loss and special controlled dielectric constant material like PTFE (Teflon) was widely used. These material was developed long time ago. Partly because of low volume in production, it is quite expensive in the past. When wireless became popular in consumer products years ago, the demand for low loss material was went high. But the material cost is still high. Even some new developed material were trying to get involved, it seems none of them can reduce the material cost dramatically. How to reduce the RF PCB cost became an essential problem for the designer. One of the solution is the mixed dielectric design.
Because the low loss material is not needed for all wireless system, it mostly designed-in, from my understanding, for the circuits from antenna to power amplifier. To reduce the PCB cost, designer used multiple PCB and only the front end of the receiver subsystem need high cost low loss material. However, the cost is still high because of multiple PCB’s and the connector between them. Beside, the Teflon PCB is soft and is comparably difficult in assembly due to warpage.
As another kind of high frequency material, Teflon pcb are widely used in wireless networks, wireless communications and satellite communications, in particular the popularity of 3G networks exacerbate the market demand for the product on the HF PCB.
What is Teflon PCB?
Teflon is a brand name for Polytetrafluoroethylene. PTFE is known for its nonstick and non-reactive surface. Teflon is a well-known material used in the manufacturing of several products. Teflon PCB is an electric circuit that is equipped with better capacities and enhanced connections.
Teflon PCB is a synthetic resin material utilized in non-sticky applications. This material is manufactured by polymerizing tetrafluoroethylene. Teflon PCB material can resist high temperatures. Due to this, it is commonly used for high-frequency PCB.
It features properties like low dissipation factor, cold resistance, low coefficient of thermal expansion, chemical resistance, and high heat. Teflon PCB manufacturers design this PCB to offer outstanding advantages to users.
Polytetrafluoroethylene is a material known for its resistance to moisture, grease, chemicals, and oil. PTFE PCB features high lubrication, no adhesion, weather resistance, and high insulation. This material is used in the production of PCB ideal for electronic appliances.
Teflon PCB in high-end electronic products uses Teflon laminate material. The scientific name of Teflon is polytetrafluoroethylene(PTFE).This material is resistant to acids, alkalis, and various organic solvents, and is almost
insoluble in all solvents. At the same time, Teflon material has the characteristics of high-temperature resistance, and its dielectric coefficient is very low, so it is an ideal high-frequency PCB material for high-frequency Teflon PCB
Teflon PCB has a series of excellent performances:
High-temperature resistance: long-term use temperature 200~260 degrees;
Low-temperature resistance: still soft at-100 degrees;
Corrosion resistance: can withstand aqua Regina and all organic solvents:
Weather resistance: the best aging life among plastics,
High lubrication: has the smallest coefficient of friction in plastics (0.04):
Non-sticky: It has the smallest surface tension among solid materials without adhering to any substance?
It is physiologically inert it has excellent electrical properties and is an ideal C-level insulating material. A thick layer of newspaper can block the high voltage of 1500V: it is smoother than ice
Teflon has outstanding excellent comprehensive properties, high-temperature resistance, corrosion resistance, non-stick, self-lubricating, excellent dielectric properties, and a very low coefficient of friction. Among Teflon PCB Teflon is a high-frequency PCB material with very excellent performance. This is very suitable for applications in radar, high-freouency communication equipment, radio equipment and other fields.
Usually in Teflon PCB general manufacturers seldom use this kind of Teflon sheet, we can provide Tefon PCB to meet customers various PCB needs. At present in the manufacture of Teflon PCB for us. Teflon PCB material can achieve 4-6 layers of pure compression: 4~8 lavers of mixed compression.
Teflon PCB Manufacturing
For the production of Teflon circuit boards, extreme attention and carefulness are required. Teflon PCB manufacturers understand that this material is different from FR4 PCB material. For the production of Teflon boards, the following should be considered;
Surface preparation: A substrate’s surface is always prepared for layer formation, marking, and metallization. The manufacturer needs to pay attention to the type of equipment utilized for the preparation of the surface.
For example, things like bristles, scrubbers, and composite brushes should be avoided during the preparation of the surface. These things can disturb the soft laminate. Sodium etchants or plasma gas recycling is used for the preparation of the PTFE surface.
Copper plating: Special care is needed when copper plating ceramic with high dielectric materials. Pure PTFE materials have a high Z-axis coefficient of thermal expansion. Therefore, it is important to utilize plated copper on through-hole walls.
This plated copper must feature high tensile strength. This helps to minimize the chances of pad lifts and barrel cracks.
Solder mask: You must apply the solder mask within 12 hours of etching the material. A Teflon PCB manufacturer must ensure it processes the etched surface via a standard PTFE cycle. You can also clean residual moisture by baking the PTFE laminates before applying a solder mask.
Drilling: This is a new procedure ideal for drilling PTFE substrates covered with copper. Drilling must be utilized with a high chip load. This removes fibers and PTFE tailing. In most cases, PCB fabricators prefer ceramic-filled laminates since they can drill them easily.
Handling and storage: PTFE laminates need extra care since they are soft. This makes them vulnerable to tearing or gouging. It is advisable they are stored at room temperature. They shouldn’t be exposed to sunlight to avoid surface oxidation and contamination.
Lamination: Teflon substrates don’t require oxide pretreatment. PCB fabricators laminate PTFE and copper films at high pressures without bonding films or pre-pegs. Sometimes, PTFE PCB manufacturers use bonding films or prepreg of a very low melting point to minimize the processing temperatures. PTFE-FR4 laminates are ideal in some applications, but they need oxide pretreatment.
Advantages of Teflon PCB
PTFE is a useful material for the fabrication of PCB. Teflon PCBs have their unique advantages.
Temperature resistance: Teflon printed circuit board can survive extreme cold and heat. This is a major reason it is used in medical applications. This board can work from -454 to 600°F and -270 to 315°F. Its ability to withstand any temperature prevents it from cracking.
Great dielectric strength: Due to the high dielectric strength of this board, it is non-conductive. It works perfectly as an insulator. The insulating capability of this material protects equipment from electrical breakdowns.
Durability: PTFE PCB is an ideal option to consider since it is very durable. It can withstand oxidation, ultraviolet rays, embrittlement, or discoloration. It is a cost-effective option because of its long-lasting nature.
Mechanically rigid: Teflon PCB is mechanically stable. This makes it ideal for use in applications that are exposed to high levels of mechanical stability. The thermal conductivity of Teflon PCB is great.
PTFE Teflon PCB to meet the demand for faster communications. Please refer Teflon PCB Applications. Teflon materials are valued for their suitability in high-frequency electronic applications. At Microwave RF PCB, FR-4 Material (approx. 4.5) dielectric constant o is often too high, its significant signal loss during transmission across the printed circuit board. Luckly, Teflon materials boast dielectric constant values as low as 3.5 or less, it is ideal material for overcoming the high-speed limitations of FR-4. The most common of these Teflon PCB materials were developed by Rogers. In addition to a reduction in dielectric constant, these materials also offer very impressive thermal characteristics for High Temperature PCB applications, reaching Tg values as high as 280°C.
Conclusion
Teflon PCB is one of the most commonly used PCBs in the electronics industry. This type of PCB has great mechanical and electrical properties. This board is used in several applications due to the benefits they offer.
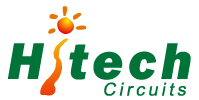
0086-755-29970700
sales@hitechpcb.com; sales@hitechcircuits.com
2F, Building C, Suojia Technology Park, Hangcheng, Bao’an, Shenzhen, Guangdong, China 518126