Through Hole PCB Assembly
What’s mean for Through Hole (THT) PCB Assembly and Surface Mount Technology(SMT)PCB Assembly ?
Surface Mount Technology (SMT) is necessary for PCB assembly. If the PCB has no through-hole components, Through Hole (THT) PCB Assembly is not needed.
SMT assembly: SMT stands for surface mount technology, which is a versatile PCB assembly technology. Currently, all electronic components can be made into surface-mounted devices (SMD). SMDs are interconnected to the PCB pads with solder paste. SMT assembly is automatic.
THT assembly: THT, or PTH or DIP, means through-hole technology. The electronic components that require THT assembly have long pins. Usually, they are capacitors, fuses, and connectors. The PCB is pre-drilled, and these components' pins plug in the holes and wave reflowed. THT assembly is manual.
In the PCB assembly process, SMT assembly happens before the THT assembly.
What are the benefits of Through Hole PCB assembly?
Through-Hole PCB Assembly comes with a range of benefits including:
Withstanding stress-As opposed to SMT components, through-hole components are known for their ability to withstand mechanical and environmental stress.
Perfect for large components-Through-hole works well for large components that have to undergo high power and high voltage
High heat tolerance-Known for their high heat tolerance, they find application in a number of industries.
Ease of Prototyping- Through-hole PCBs also lend themselves to ease of prototyping and improved reliability
High Reliability-Through-hole PCBs are best used for high-reliability products that require stronger connections between layers.
Little surprise then, that even though surface mount components allow for denser configurations, for larger and heavier components that require strong bonds, through-hole technology has remained resilient and relevant.
What are the capabilities you offer for Through Hole PCB assembly?
We provide through-hole PCB services to a variety of industries including medical, electronics, instrumentation, etc, all thanks to our complete assembly capabilities:
• Hand soldering
• Dual wave flow solder
• Hand Insertion of components
• Automate axial or radial insertion
• RoHS soldering using tin-lead solder
• Use of high and low melting point solder
• Prototype build to high-volume assembly
• Functional test and automated inspection
• Support various types of PCBs including metal core PCBs, Rigid PCBs, Flex-rigid PCBs, FR4 PCBs, etc.
Disadvantages of Through Hole Assembly
Like any other manufacturing or assembling techniques, Through Hole PCB Assembly has its disadvantages too.
These include:
Longer production time-It takes a lot of time to drill the multiple holes through which the leads are expected to run.
Expensive-because the drilling process is difficult and time-consuming, it increases the cost of production
Minimizes space on the boards-drilling the holes on the surface of the board limits the routing area for tracing signals.
Also, by feeding the leads through the board, only one of its sides is usable, thus making the THT PCB a bit slower in operation speeds.
Through Hole Assembly Components – What are the Best Components for Through Hole Assembly?
Radial lead components
Axial lead components.
Types of Through Hole PCB Assembly
There are two (2) main types of the Through Hole PCB Assembly. The first is the Automated Through Hole PCB Assembly. The second is the Manual Through Hole PCB Assembly.
On the one hand, the automated variant is roundly touted to be faster and cost-effective because it takes little time to be completed. It also demands little human inputs, which makes it cost-effective.
On the other hand, the manual Through Hole PCB Assembly involves the traditional or manually-operational model of drilling the holes into the Printed Circuit Boards (PCBs). This model tends to take time and attracts more costs.
Functional tests and automated inspection for Through Hole PCB Assembly
Using automated inspection is very critical in minimizing turnaround time to ensure timely delivery of the boards.
Conclusion
As you can see, Through Hole Assembly of PCB can be time consuming.
However, in some applications, it is worth it more so when mounting heavier and bulkier components.
You can easily achieve the strength by soldering the components on the reverse side as you have seen.
In fact, it is virtually impossible to pull components assembled using Through Hole Assembly.
The good news, today’s guide has simplified the Through Hole PCB Assembly technique.
Do you have questions or inquiries on Through Hole Assembly process?
Contact us now. sales@hitechpcb.com
In addition to through hole PCB assembly, we also provide value-added services, such as conformal coating, labeling, and complete PCB encapsulation.
Through-hole PCB Assembly Testing and Inspection at Hitechpcba
In-Circuit Testing:
This type of testing is conducted for high volume production lines, and helps us check every minute soldering and other components in detail.
Automated Optical Inspection: Abbreviated as AOI, these tests are performed to ensure that product is free from soldering, component, and BGA defects.
Automated X-Ray Inspection(AXI):
This testing is performed to inspect insufficient fills, short circuits, fills, etc. The automated X-ray inspection helps reduce the number of defects and improve the quality of the Through-Hole circuit.
Burn-in Tests:
These tests detect components’ failure or reliability in real environments.
Assisted Visual Inspection:
Our experts use a wide range of advanced visual inspection equipment to perform a detailed inspection of soldering and component placement accuracy.
What’s difference between SMT assembly and THT assembly?
Most contract PCB Assembly manufacturers concentrate on their surface mount technology capabilities for PCB assembly. The SMT lines can be almost completely automated making it possible to run a high volume of boards with little human intervention and a low cost per board. Through whole assembly whether automated or manual is a slower process, it takes resources away from the high-volume business that many manufacturers prefer.
Only about 10 percent of the parts we buy are through-hole. Nearly 75 percent of the boards we run are mixed technology, which is a combination of through-hole and SMT parts one reason for this is that nearly half of our board assemblies are for high powered boards which use capacitors inductors and transformers to transfer energy. The size of these components is proportional to the energy they can store so for a high-power board we need to use some fairly large and heavy components and that means through-hole technology, in addition things like customer accessible connectors, that have to withstand stress as cables are connected and removed are likely to be through-hole components. Through-hole components are held in place by the pins as well as the solder so you can get a much stronger and more reliable mechanical bond than with surface mount components that have only solder to hold them in place. If a contract manufacturer is focused on higher volume SMT business, it's important to understand how they will handle through-hole components when you need them at z-axis. We run mixed technology boards every day we have a modern stuff line with a paperless process for assembly instructions and assemble in a single piece flow from the stuff line to a wave solder to inline inspection, d-paneling, qc testing.
In addition to PCB Assembly, be it through hole or surface mount, at Hitech Circuits Co., Limited we also undertake PCB assembly rework offering complete reliability, high quality and optimal costs. Not only are we well-versed in inventory management, fabrication and process control, we also have a stringent control on vendor component management.
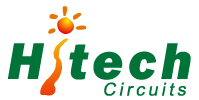
0086-755-29970700
sales@hitechpcb.com; sales@hitechcircuits.com
2F, Building C, Suojia Technology Park, Hangcheng, Bao’an, Shenzhen, Guangdong, China 518126