Flexible PCB and its Material, FPCB Design, Manufacturing, Advantages and Applications
What’s Flexible PCB?
Flexible PCB or FPCB is known to be a type of circuit board with many advantages. Most flex PCBs are multilayer PCB.
Compared to traditional rigid PCBs, flex PCB designs usually are more complex and challenging. This type of board can be designed in various ways to achieve the ideal shape for packaging. The flex PCB shape can be in the product when installed.
A flex PCB is unlike any other type of electronic device. It features a combination of thin and flexible substrates and a single component, making design incredibly challenging. When designing the first rigid-flex board, most of the designers had no idea what to expect when it came to designing PCBs.
Printed circuit boards made from rigid flex joints are no longer two-dimensional plane bottom boxes. Instead, they feature a three-dimensional internal structure that allows them to be bent and folded. As a result, this new type of electronic device has a more robust performance and is more stable than traditional PCBs. In addition, the designers of these boards use a single component, eliminating the need for multiple cables and connectors.
Why Did Flex PCB Come into Play?
Flex PCBs have arisen to tackle the growing need for more efficient and cost-effective electronic components.
Flexible circuit boards are incredibly versatile because they can be bent and flexed, allowing them to fit into tight spaces that would otherwise be inaccessible with traditional rigid circuit boards.
Flex circuits also provide enhanced protection against vibration, shock, and other environmental factors that can cause damage to traditional rigid circuit boards.
They are also often more lightweight than their rigid counterparts, which explains why they are ideal for use in aircraft or aerospace applications where weight is a significant factor.
Flexible printed circuit boards are used in various applications, from medical devices and automotive systems to consumer electronics.
Flex PCBs are becoming increasingly popular, given that they can provide reliable performance in challenging environments while still offering cost-effective solutions.
They also offer all sorts of customization options, allowing for higher levels of performance and design flexibility than traditional rigid circuit boards. Undoubtedly, the flex PCB has a bright future. Thanks to advances in technology and materials, flex PCBs are becoming more reliable and cost-effective. It’s no wonder why they are regarded as an excellent choice for many industries.
Materials of Flex PCB
Substrate and Protective Film
Printed circuit boards commonly used for electronic products are made from glass fibre and epoxy resin. Although rigid is often used to describe these boards, they can feel their elasticity even if one removes a single layer. Due to the cured epoxy resin, these boards can be more rigid, but they cannot be used for specific products because it is not flexible enough. Nevertheless, some products need PCB with this property. It is why it is ideal for those products that are only assembled.
In addition to being used for electronic products, Flexible plastic film is also commonly used in various applications. One of the most common types of plastic film is polyimide, which is very soft and firm. In addition, due to its thermal stability, it can endure temperature changes during reflow welding and resist the effects of deformation and expansion.
Another flexible material type is polyester, commonly used in electronic equipment. Compared to polyimide film, its temperature deformation and heat resistance are worse. This material is usually wrapped in soft films, ideal for printing circuits. Since it cannot withstand high temperatures, cold pressing makes these flexible circuits.
The display part of a clock radio uses a Flexible connection circuit, often working abnormally. The leading cause of this issue is the poor quality of the connector. We recommend using PI film for flex-rigid PCBs to solve this issue.
For flexible circuits, such as those used in electronic devices, various materials, such as PET, PI, and glass fibre core, are used to protect the conductor. In addition, the circuit may also need to use other protective films, such as those designed to protect against corrosion and damage. These can be used to mask solder resist ink. In addition, the insulating film can help prevent the conductor from getting damaged or corrosion.
PET and PI film have a thick film thickness of around 1/3 to 3 mil. The film’s other options are fibreglass or epoxy, typically thicker at 2 to 4 mils.
Although FR4 materials are commonly used for rigid boards, many requirements must be considered when combined with rigid-flex materials.
Someone may claim, “ It’s better to choose the substrate and the covering film with a smaller size contraction and expansion for the materials of flex PCB, right?” Yes, what a point!
Highly flexible and temperature-resistant, polypropylene polyimide (PI) is commonly used in flexible substrates. Its advantages include good mechanical and electrical properties, good moisture absorption, and good weather resistance. But, you may wonder, “Is polyesterimide the most commonly used type?” The answer is yes.
Polyester PET is cheap and has good tear resistance, flexibility, and mechanical properties. Unfortunately, this material’s disadvantages become apparent when heated, as follows.
A significant shrinkage rate
Not ideal for high-temperature soldering due to its high-temperature resistance
Coverlay
Readers familiar with the PCB industry may question, “The purpose of a covering film with a thickness of around 1/2mil to 5 mils is to protect a circuit from moisture, pollution, and soldering. Is that right?” Yes, what a good guess!
The covering film on a PCB is often composed of polyimides, polyester, or polyethylene. The film serves as a mechanical and environmental barrier that protects the copper surfaces from damage during assembly and operations. Depending on the application, the thickness of the protective layer can range from 0.5 mils to 5 mils.A reinforcing film is used to cover a Flex PCB when it’s needed for welding or adding reinforcement. It can be made from various materials such as aluminum, steel, and FR4.
The low-flow PP is commonly used for covering flex-rigid bonding PCBs, such as the Flex-Connect and Rigid. Usually, there are three specifications for this material: 106 (2mil), 1080 (3mil), and 2116 (5mil).
A coverlay film is used to provide excellent mechanical and electrical protection. It’s typically made of polyimide or polyester, which has superior heat resistance and high dielectric properties compared to PP. The thickness of this protective layer can range from 0.5 mils to 5 mils.Most electronic products commonly used for money-saving activities, such as the printing of wires, are still made with copper wire. However, copper foil can be used in different forms when replacing wires and connectors. For instance, copper foil can be the best choice if only to replace the connectors and wires.
In addition, when it comes to improving the carrying capacity of a device, such as a conductor, copper foil can be used by increasing its weight. This material can also achieve a copper sheet width of 1x.
Finally, copper foil is often used to enhance the ability of an insulation material due to its high-frequency characteristics. This allows for better shielding and a reduction in electrostatic interference. Copper foil can also be used as a protective layer between components due to its low-resistance and high dielectric properties compared to PP.Unfortunately, copper is known to be poor at work and causes stress and fatigue. If a flexible circuit needs to be repeatedly shifted or folded to maintain its structural integrity, then copper foil can be the best choice. However, due to its rolling toughness, it can be bent and folded more frequently before fatigue fractures occur.
The increased elasticity of copper foil when it’s rolled can also be used to improve its mechanical properties. For example, this material can extend the life of a Flexible circuit by increasing its rolling toughness.
Adhesive
In addition to copper foil, we must apply adhesive to other films, such as PI film. Due to the different properties of copper foil, such as its hardness, it is impossible to achieve good bonding at high pressure and temperature. Some manufacturers provide copper-clad laminates that are double and single-sided. They use a thickness of one to two mil or one mil of epoxy or acrylic adhesive. It is specially developed for FPC. Due to the increasing popularity of “Glue free” laminates, the need for more efficient processing techniques has led to the development of new materials, such as copper skin on PI films. These materials can be used in large-scale HDI PCB circuits. We will use hot melt, silicone, or epoxy resin when protecting the Flex rigid joints. These two materials will help improve the mechanical strength of the joints and prevent them from experiencing stress fatigue.
Structural Form of Flex PCB
Flex PCBs consist of a thin substrate material with laminated copper conductor layers. Flex circuits can be designed with different configurations, including single-sided, double-sided, and multi-layer boards.
According to Hitechpcb’s experience, flexible circuit boards are typically constructed using three layers of material: an upper core layer made from polyimide or other flexible plastic, an insulating middle layer of either epoxy or silicone; and a bottom conductor layer made of copper. The layers are laminated together using heat and pressure. Flexible printed circuit boards can also be constructed with additional layers to add functionality, such as special shielding for electrical noise or extra conductive circuits for more complex applications.
Production of Flex PCB
The manufacturing process for flexible circuit boards is complex and involves several steps. The first step is to create the circuit design, including components and traces. It can be done either manually or using computer-aided design (CAD) software. Once complete, the design must be printed onto a flexible substrate, typically polyimide film or another similar material. Flexible substrates are ideal for flex PCB production because they allow for curved shapes and thinner trace widths, which are necessary for miniaturization. After the circuit design is printed onto the substrate, it must be cut to size and then laminated with copper foil. Once complete, the flex printed circuit boards are ready for automated assemblies, such as soldering components or attaching connectors.
Flexible PCBs are a versatile and cost-effective way to produce small, lightweight electronics that increase flexibility and reliability. By following the steps outlined above, flex PCB manufacturers can create reliable flex circuits quickly and efficiently. This guide lets you understand how they work and why they are essential to modern electronics production.
Layout of Flex PCB
The design of flex PCBs is complex. Due to the varying signals and energy transmission, it is crucial to consider the various factors that affect the system.
The layout principle of flex PCBs should be followed to minimize the system’s complexity. In addition, the layout of the core components and the essential unit circuits should also be prioritized. The layout should also be arranged according to the signal flow direction of the board.
The overall wiring of the board should be as short as possible. The critical signal lines should also be as short as possible. The decoupling capacitor should be placed as close to the pin of the power supply as possible. The loop connecting the ground and the power supply should also be the shortest. The signal should be run in the correct direction to prevent accidents.
The arrangement of the components should also be convenient for maintenance and debugging. For example, significant components should be placed away from small ones to avoid getting too crowded. Also, there should be enough room around the components to allow debugging.
For circuits with the same structure, the “symmetrical” standard should be adopted as far as possible. In addition, the layout should also be optimized according to the gravity balance and uniform distribution. Founded in
The electronic industry’s leading online supplier of components, sensors, and printed circuit boards (PCBs) can provide a comprehensive solution to the electronic industry’s supply chain needs. In addition, it allows customers to manage their various requirements through a single platform.
In addition to the usual layout principle, the orientation of the components should also be changed according to the type of board. For instance, the orientation of the plug-in components should be in the X or Y direction.
The heating components should be evenly distributed to minimize the heat generated by the machine and the single board. In addition, temperature-sensitive components should be placed away from significant heat sources.
The signals from high, low, and high currents are entirely separated. In addition, the signals from digital and analog are also separated. Therefore, the high-frequency and low-frequency components should be spaced adequately. It should be noted that the same power supply should be used to place all the components together to facilitate the separation of the power supply in the future.
The layout principle is the most critical aspect of designing a circuit. It involves the placement of the various components and their connection. The priority of the vital signal line should be given to the signals that are most important to the design, such as the small signal, high-speed signal, and synchronization signal.
The density priority principle should also be followed to start wiring the components from the most complex connections on the board.
Considerations for Design Rules of Flex PCB
Compared to the traditional printed circuit board design, the flexible circuit board design is more complex. That’s why the appropriate rules must follow the various aspects of the design. For instance, the transition area and the routing of the board are required to follow the rules of the corresponding design rules.
Through Hole Position
When the flex PCB is bent in dynamic use, the vias should be avoided as much as possible. These are easy to crack and are often the cause of damage. Some people may wonder, “Can we take some measures? For instance, holes can also be punched in the flexible circuit board’s strengthening area, and do not cross the edge line of this area, is that right?” Yes, you are right. It means that when designing flex PCBs, a certain distance should be avoided from the combination area.
The flex-rigid joint area design specifications and the through hole are specified to follow a certain distance. For high-performance applications, the limit is usually set at around 70mil. For processing manufacturers, the limit for vias should be at least 30mil. Follow these rules for both flex and vias. It is the most important rule regarding the combination of Flexible boards.
Design of Pads and Vias
Flexible PCBs require careful consideration when designing the pads and vias. Flexible PCBs are constructed with a non-rigid substrate material, usually polyimide or polyester, allowing them to bend and twist without breaking. However, this flexibility comes at a cost; since the material is not rigid like traditional FR4 substrates, the pads and vias require more precision to ensure they can withstand flexing.
Flexible PCBs often call for unique pad shapes or sizes and special soldering techniques to maximize durability and performance. There is also a need for extra spacing between components and circuitry to prevent short circuits due to strain on the board. These considerations must be considered when designing a flexible PCB, as they will determine the final product’s success. Engineers can produce reliable and effective printed circuit boards by understanding the additional complexities involved with flex PCBs and taking appropriate steps to ensure all design elements are optimized for flexibility.
Routing Design
If there are multiple lines in the Flex area, try to avoid overlapping the paths of the top and bottom layers of the copper wire sheet. It can cause inconsistent stress on the line, leading to mechanical damage. Instead, the paths should be staggered, and the upper and lower layers should be arranged in a straight line.
The design of the Flexible area is similar to that of the rigid area, except that instead of following an angled line, it should follow a circular arc. It can help protect the Flexible board’s lines from getting damaged while bending. The thick and thin lines should also be connected with teardrop-shaped arcs to avoid sudden contraction or expansion.
Copper Laying Design
Some may wonder, “For flexible bending reinforced panels, using a mesh structure with a copper plane layer or lay-up is generally better. Is that right?” The answer is yes. However, for applications such as control of electrical resistance, the electrical quality of the reticulated structure needs to be better. Therefore, the designer should make an informed decision regarding using the reticulated copper sheet. For instance, if the waste area is covered with solid copper paving, the designer should consider designing more solid copper paving.
Distance Between Drilling Hole and Copper Sheet
According to Hitechpcb’s experience, flexible printed circuit boards can accommodate greater distances between the drilled holes and the copper board than conventional rigid boards. The explanation is that the flexible materials used in their construction allow for more complex designs with more detail. As a result, creating designs that necessitate more clearance or space for components can be helpful.
Bending Radius of Bending Area of Flex PCB
As our engineers suggest, the bending radius of the printed circuit board affects the overall performance and reliability of the PCB, given that it determines the amount of pressure which is being applied to the components on the board. Therefore, based on experience, Viaison would design flexible PCBs with suitable material and the correct bending radius to maintain their shape and performance.
Pros and Cons of Flex PCB
Advantages
Flex PCBs allow for greater design flexibility, allowing components to be placed in various configurations.
Flexible circuit boards are much thinner than traditional rigid boards and can conform to almost any shape or space.
Flexible printed circuit boards are lighter, making them easier to transport or install.
They can also reduce the time and cost associated with assembly due to their ability to be easily bent into place without requiring extra hardware or soldering.
Flex circuits are more resistant to shock and vibration because they absorb impact better than other boards.
Flexible PCBs use less material, making them cheaper than other printed circuit boards (PCBs). This results in lower overall costs for production runs requiring many units simultaneously.
Disadvantage
Flex PCBs have some notable disadvantages compared to standard rigid boards. Hitechpcb summarizes the following points.
Flexible PCBs are more expensive than rigid PCBs thanks to their design and manufacturing complexity.
Flex circuits can be more prone to manufacturing defects due to the nature of their construction. Flexible boards require extra testing and QC to ensure the product is made correctly.
Flexible circuit boards require specialized materials and expertise, making them less accessible to small businesses or hobbyists.
Flexible printed circuit boards are less reliable than rigid boards due to their tendency to flex, bend, and twist under pressure or vibration. The same force may cause damage to a flexible board that would not affect a rigid board.
Flexible PCBs require more complex soldering techniques, which can result in reduced yields and increased production costs.
Application of Flex PCB
Wearable Electronics
Flexible Displays
Automotive Applications
Flexible Lighting Solutions
Flexible Heating Elements
Medical Devices and Robotics
Aerospace and Defense
Applications
Solar Panels and Wind Turbines
Industrial Controllers and Sensors
Flexible Implantable Electronics
Conclusion
Flexible PCBs are a great way to add functionality and efficiency to your product designs. So whether you’re looking for greater product design flexibility or more reliable and efficient solutions, it is worth considering integrating flexible printed circuits into your next project. Hitechpcb is a leading flex PCB manufacturer which can provide high-quality flexible PCBs. Welcome to cooperating with us!
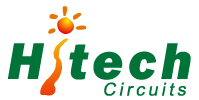
0086-755-29970700
sales@hitechpcb.com; sales@hitechcircuits.com
2F, Building C, Suojia Technology Park, Hangcheng, Bao’an, Shenzhen, Guangdong, China 518126