Rigid Flex PCB Circuit Board Technology
Rigid Flex PCBs have become increasingly popular in the electronics industry due to their ability to combine the benefits of both rigid and flexible PCBs. These unique circuit boards are designed to be bent or folded, allowing for greater flexibility in product design and space-saving opportunities. However, one critical aspect that must be carefully considered when working with rigid flex PCBs is the calculation of the bend radius.
In this article, we will explore the factors that affect the bend radius calculation for rigid flex PCBs. Understanding these factors is essential for ensuring the reliability and functionality of the PCBs during bending operations. We will discuss the various methods available for calculating the bend radius, allowing designers and manufacturers to make informed decisions based on their specific project requirements.
Factors such as the thickness and material properties of the PCB, the number and type of conductive layers, and the intended bending angle all play a significant role in determining the appropriate bend radius. By considering these factors, designers can prevent issues such as cracking, delamination, or failure of the conductive traces during the bending process.
Additionally, we will delve into the different methods used to calculate the bend radius for rigid flex PCBs. These methods range from simple guidelines based on the PCB thickness to more complex mathematical formulas that take into account the specific material properties and bending conditions.
By understanding the factors affecting bend radius calculation and utilizing the appropriate methods, designers and manufacturers can ensure the reliability and longevity of their rigid flex PCBs. This article aims to provide a comprehensive overview of the bend radius calculation process, enabling professionals in the electronics industry to make informed decisions and produce high-quality products.
Factors Affecting Bend Radius Calculation
When it comes to designing and manufacturing Rigid Flex PCBs, one important aspect that engineers need to consider is the bend radius calculation. The bend radius refers to the minimum radius that a flexible circuit can be bent without causing damage or affecting its performance. There are several factors that can affect the bend radius calculation, and understanding these factors is crucial for producing reliable and durable Rigid Flex PCBs.
The first factor that affects the bend radius calculation is the thickness of the base material. Thicker base materials tend to have larger bend radii because they are less flexible. On the other hand, thinner base materials can be bent more easily and therefore have smaller bend radii. It is important to select the appropriate base material thickness based on the specific requirements of the Rigid Flex PCB design to ensure optimal flexibility and reliability.
Another factor that influences the bend radius calculation is the number and type of copper layers in the PCB. The copper layers provide the electrical connections and contribute to the overall rigidity of the board. If there are multiple copper layers in the Rigid Flex PCB, the bend radius needs to be larger to prevent any damage to the copper traces or vias during bending. Additionally, the type of copper used, such as standard copper or high-temperature copper, can also impact the bend radius calculation.
The flexibility of the coverlay material is yet another factor that affects the bend radius calculation. The coverlay material is a protective layer that is applied to the flexible circuit to protect the copper traces and provide insulation. The flexibility of the coverlay material can vary depending on its composition and thickness. A more flexible coverlay material allows for smaller bend radii, while a less flexible coverlay material requires larger bend radii to avoid cracking or delamination.
Furthermore, the overall design of the Rigid Flex PCB, including the placement of components and the routing of traces, can influence the bend radius calculation. Components that are located close to the bending area may require larger bend radii to prevent any interference or damage. Additionally, the routing of traces should be carefully planned to avoid sharp angles or tight bends that could cause stress concentration points and lead to failure during bending.
Methods for Calculating Bend Radius
Calculating the bend radius is a crucial step in designing and manufacturing Rigid Flex PCBs. The bend radius refers to the minimum radius that a Rigid Flex PCB can be bent without causing any damage to the components or the circuitry. It is important to calculate the bend radius accurately to ensure the reliability and functionality of the Rigid Flex PCB.
There are several methods for calculating the bend radius of a Rigid Flex PCB. One common method is to use the IPC-2223 standard, which provides guidelines for calculating the bend radius based on the thickness and the number of layers of the Rigid Flex PCB. This standard takes into account the material properties and the mechanical stress that the Rigid Flex PCB will undergo during bending.
Another method for calculating the bend radius is to use the formula R = t × K, where R is the bend radius, t is the thickness of the Rigid Flex PCB, and K is a constant value that depends on the material properties. This formula provides a general estimation of the bend radius and can be used as a starting point for further analysis and optimization.
In addition to these methods, it is also important to consider the specific requirements of the application and the manufacturing process. For example, if the Rigid Flex PCB will be subjected to repeated bending or if it needs to fit into a tight space, a smaller bend radius may be required. On the other hand, if the Rigid Flex PCB will be used in a high-temperature environment or if it needs to support heavy components, a larger bend radius may be necessary.
It is worth noting that calculating the bend radius is not only about meeting the minimum requirements but also about optimizing the design for maximum reliability and functionality. This involves considering factors such as the material properties, the number and type of layers, the placement of components, and the routing of traces. By carefully considering these factors and using the appropriate calculation methods, designers and manufacturers can ensure that the Rigid Flex PCB will perform well under bending and meet the specific requirements of the application.
Conclusion
The article emphasizes the importance of accurately calculating the bend radius in the design and manufacturing of Rigid Flex PCBs. Several factors, such as the base material thickness, copper layers, coverlay material flexibility, and overall design, affect the bend radius calculation. By considering these factors and using appropriate calculation methods like IPC-2223 standard or the R = t × K formula, engineers can ensure the production of reliable and durable Rigid Flex PCBs that meet specific application requirements. Designers and manufacturers should also optimize the design to achieve maximum performance and meet the desired bend radius by considering the application requirements and manufacturing process.
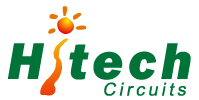
0086-755-29970700
sales@hitechpcb.com; sales@hitechcircuits.com
2F, Building C, Suojia Technology Park, Hangcheng, Bao’an, Shenzhen, Guangdong, China 518126