Electronic Manufacturing
What is Electronic Manufacturing Service?
Electronic manufacturing services are also called electronic EMS, electronic contract manufacturing. If the company announces they provide an electronics manufacturing service, it can provide service of electronics design, manufacturing, testing, distribution, storage, logistic, return/repair, etc.
Electronics Manufacturing Services (EMS) providers are those companies that provide both original equipment manufacturers (OEMs) and end-users with electronic products and services. These include PCB and electronics design, manufacturing, testing, supply chain management, and repair and maintenance.
Hitechpcba is a trusted EMS provider in China. We focus on small to medium-volume PCB and electronics device manufacturing with more than 20 years of experience. Our factory is UL-listed, ISO9001, IATF16949 and ISO13485 certified.
Our electronic manufacturing capabilities:
PCB Fabrication
PCB assembly
Consigned PCB Assembly
Turnkey PCB Assembly
Electronics Parts Sourcing
Box Build Assembly
IC Programming
PCBA Functional Testing
Cable/wire harness assembly
Conformal coating
Repair/Rework services
Reverse engineering services
Labeling & Packaging
Customized Logistics Per Customer
The Process of Electronic Manufacturing Services-12 Steps
1. DFM/DFA
PCB file checking
PCB file checking is an essential step in the PCB manufacturing process. It involves verifying that all elements of a PCB design have been appropriately created and placed to ensure that it meets the customer's requirements.
PCB file checking also ensures that errors or mistakes are identified before production begins, thus avoiding costly delays or rework. As a result, manufacturers can guarantee quality control throughout their production process through thorough PCB file checking.
BOM list check
BOM list check is an essential step in the electronic manufacturing process. It ensures that all of the components used in a product are present, accounted for, and fit for purpose. BOM list checks also help identify discrepancies between what has been ordered and delivered to the production line.
By thoroughly checking BOM lists before assembly begins, manufacturers can ensure that their products are made with quality components and materials. Without a BOM list check, it's impossible to manufacture higher-quality finished goods with fewer defects or problems down the road.
2. PCB Fabrication & Parts sourcing
PCB Fabrication
PCB fabrication is the process of creating printed circuit boards (PCBs). PCBs can be made with different materials and techniques, depending on the application they will be used for.
The fabrication begins by designing a PCB layout that meets the device's specifications. Once this design is complete, it must be manufactured to create an actual board.
The following steps involve etching copper onto a substrate such as a fiber glass or ceramic, drilling holes for components and connections, and then soldering components into the board.
After these steps are completed, PCB testing must occur to ensure functionality before it can be sent off for use in its intended device.
PCB fabrication is a complex but necessary process that must be done precisely to ensure the PCB works as expected.
Electronics Parts sourcing
Electronics parts sourcing is locating and supplying electronic components, such as semiconductors, resistors and capacitors, for use in electronic devices.
It involves researching suppliers that offer quality products at competitive prices, negotiating pricing and delivery terms, and ensuring components meet safety regulations.
As electronics become increasingly complex, electronics parts sourcing has become essential to the engineering process.
By outsourcing this task to experts who understand the complexities of electronics parts sourcing, businesses can ensure they are getting reliable supplies at reasonable costs. Additionally, electronics parts sourcing professionals can provide valuable insight into the latest trends in electronics components and help ensure that any new electronics designs comply with relevant safety regulations.
Ultimately, electronics parts sourcing allows businesses access to the components they need when they need them at a price that works for their budget.
3. PCB Assembly
SMT assembly, or Surface Mount Technology assembly, is an electronic manufacturing process that involves placing components onto a printed circuit board (PCB). SMT is one of the most widely used methods in modern electronics production thanks to its low cost and high efficiency. SMT assembly requires specialized tools and processes for mounting components on both sides of the PCB at once. This method offers excellent flexibility regarding component placement and improved electrical performance over traditional through-hole technology. SMT also allows for faster turnaround times compared to other electronic assemblies, given its automated nature and advanced automation solutions such as pick-and-place machines. SMT assembly is especially suited for high-volume production, which explains why it is highly sought-after for large-scale manufacturing.
PTH assembly, or Plated Through Hole assembly, is a method of mounting electronic components onto printed circuit boards. PTH assemblies typically comprise pins inserted into the board’s holes and then soldered in place. PTH assemblies provide robust mechanical connections for electrical components, making them ideal for high-reliability applications such as automotive electronics or medical devices. PTH assemblies can also create complex circuits with multiple layers of copper traces and pads on both sides of the board. With proper design and quality assurance procedures, PTH assemblies offer reliable performance over a long service life while providing cost savings due to their relatively low material costs compared to other soldering techniques.
4. IC programming
IC programming is an essential part of electronic manufacturing, playing a crucial role in developing and producing devices such as smartphones, computers, and other consumer electronics.
IC programming involves writing code that tells integrated circuits (ICs) how to behave when installed in a device. This code can include instructions on how the IC should interact with other components within the system and the tasks it should perform.
IC programming is also used for testing during design verification and debugging, ensuring that ICs are functioning correctly before being shipped out to customers.
With its importance across many industries, IC programming has become an invaluable skill set for those looking to break into or advance their careers in electronic manufacturing company.
5. PCB Testing & Inspections
AOI inspection
AOI (Automated Optical Inspection) is a vital part of the electronic manufacturing process. AOI inspection is a non-destructive testing method to detect and identify printed circuit board (PCB) defects. It involves using optical technology such as cameras, lasers, or X-rays to scan each component on a PCB for abnormalities. In addition, AOI systems can be programmed to look for specific types of defects, including missing components, incorrect polarity, shorts between pins, misalignments between layers, and other issues that could cause product failure. Undoubtedly, AOI inspection provides manufacturers an efficient way to quickly and accurately identify potential problems before products are sent out for final assembly or packaging, in Hitech Circuits, for all PCBA we do AOI inspection.
Visual inspection
Visual inspection is a crucial process in electronic manufacturing company, as it helps to ensure that the electronic components being produced meet high standards of quality. Visual inspection involves examining electronic components and assemblies closely for any potential defects or inconsistencies affecting their performance or reliability. This type of inspection requires careful observation, attention to detail, and an understanding of the technology involved to identify any irregularities quickly. By using visual inspection methods, manufacturers can detect issues before they become more serious problems down the line.
In-circuit Test
In-circuit test (ICT) is electronic manufacturing testing that checks for electronic components and circuits’ correct functionality and physical integrity. It is an important quality assurance tool in electronic product development, production, and repair. ICT involves connecting a specialized test system to the electronic circuit board under test and then running tests to detect errors or defects in the parts or their connections on the board. This process helps manufacturers ensure that their products meet design specifications before they are released into the market.
6. Electro-mechanical assembly
Electro-mechanical assembly is a crucial part of electronic manufacturing, given that it combines electronic and mechanical components to create more complex systems. By combining electrical circuits with physical components such as motors, actuators, sensors and other devices, electro-mechanical assemblies can produce highly efficient products used in various industries. However, this process requires a combination of engineering knowledge and skillful craftsmanship to ensure the accuracy of each electronic product. With advances in technology and automation, the electro-mechanical assembly has become increasingly popular for its ability to reduce production time while increasing quality control.
7. Functional Test
A functional test is essential to EMS manufacturing, ensuring the electronic product meets the required specifications and functions correctly. The functional test involves testing each device component to ensure they work perfectly together. That includes testing for compatibility, performance, reliability and safety features. By performing Functional Tests on electronic products during production, manufacturers can save time and money by avoiding costly defects or recalls later.
8. Burn-in Test
Burn-in Test is an EMS manufacturing process used to test the reliability of electronic components. It involves running a device or system under normal operating conditions for a while, usually with simulated environmental conditions such as temperature and humidity. That allows for identifying and correcting any potential defects or problems that may arise during prolonged use before the final product is released. By doing so, the burn-in test helps ensure that electronic products function reliably over their expected lifetime.
9. Wire bonding
Wire bonding is a critical process in EMS manufacturing, allowing for the secure connection of electronic components. That involves joining two pieces with an electrical wire from gold or aluminium. Wire bonding can join multiple electronic components, ensuring they are securely connected and functioning correctly. The most common type of wire bond is a ball bond, where the wire is shaped into a small sphere at each end which makes contact with both electronic components being joined. There are also other types of bonds, such as wedge or stitch bonds, which may be used depending on the project's needs. Wire bonding provides a reliable connection between electronic components while ensuring they remain electrically isolated and operate without interference.
10. Conformal Coating
Conformal coating is an electronic manufacturing process that protects electronic circuits from extreme environmental conditions. This protective coating helps prevent the corrosion and oxidation of electronic components and provides a barrier against dust, moisture, fungus, and other contaminants. Conformal coating can also provide electrical insulation between components on a circuit board or other substrate.
11. Final Quality Control (FQA)
Final Quality Control (FQA) is an essential step in EMS electronics. It involves inspecting and testing electronic components, assemblies and products to ensure they meet pre-defined quality standards. FQA helps identify potential defects or issues that could affect product performance before reaching the end user. By implementing rigorous FQA procedures, electronic manufacturers can guarantee high levels of quality assurance throughout their production process and reduce costly recalls due to faulty parts or products.
12. Custom Packaging
Custom packaging in EMS electronics is the process of designing and fabricating a unique package that meets the needs of a specific electronic product. This type of packaging is essential for protecting electronic components from environmental hazards such as dust, moisture, vibration, shock, and temperature extremes. Custom packaging also helps reduce costs by providing an efficient way to store and transport electronic products safely. Additionally, custom packaging can help improve product performance and reliability by reducing the risk of damage during handling or shipping. Undoubtedly, manufacturers can ensure their electronic products are correctly packaged while saving time and money on production costs by utilizing custom design techniques.
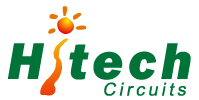
0086-755-29970700
sales@hitechpcb.com; sales@hitechcircuits.com
2F, Building C, Suojia Technology Park, Hangcheng, Bao’an, Shenzhen, Guangdong, China 518126